Summary
This article explores the future of motion control systems, highlighting emerging trends that are crucial for enhancing precision machinery`s efficiency and reliability. Key Points:
- AI-driven predictive maintenance enhances performance by anticipating system failures and adjusting controls in real-time.
- Quantum computing offers groundbreaking optimization methods for complex motion control challenges, improving efficiency beyond classical capabilities.
- Haptic feedback systems facilitate intuitive human-robot collaboration, ensuring safer and more effective industrial applications.
What Drives the Evolution of Motion Control Systems in Precision Machinery?
Why is the integration of quantum technologies set to revolutionize motion control systems in precision machinery? With the relentless pursuit of sub-nanometer precision, 70% of companies are adopting these advanced methods, yet many remain unaware of their potential. This isn't mere speculation; it's a transformation currently underway that promises a paradigm shift in accuracy and control. However, as we strive to implement these groundbreaking innovations, things often become more complex than anticipated…
My First Encounter with Motion Control: A Story of Frustration and Learning
My first real experience with motion control was during a group project in college. It was a rainy Tuesday afternoon in March 2023, and I walked into the lab, feeling pretty optimistic. “Just wire up the servos to the controller,” my professor casually mentioned. But—well, things didn’t quite go as planned.
After two hours of fiddling with wires and connectors, nothing happened. “Why isn’t it responding?” I mumbled, frustration creeping in. My teammate Sarah leaned back in her chair, exasperated. “Did we check the code? Maybe there’s a glitch?” We both stared at the screen—a jumble of lines that seemed more like hieroglyphics than helpful instructions.
As the clock ticked towards 6 PM, panic set in. Three attempts later and error messages were flashing like confetti on New Year’s Eve. “Seriously? This shouldn’t be this hard,” I thought bitterly while surveying our chaotic workspace littered with tools and parts.
“Do you think we’ll actually finish this by Friday?” Sarah finally asked, eyebrows raised in disbelief. The weight of uncertainty hung heavy between us; it felt impossible—like we were racing against time without even knowing where to start.
After two hours of fiddling with wires and connectors, nothing happened. “Why isn’t it responding?” I mumbled, frustration creeping in. My teammate Sarah leaned back in her chair, exasperated. “Did we check the code? Maybe there’s a glitch?” We both stared at the screen—a jumble of lines that seemed more like hieroglyphics than helpful instructions.
As the clock ticked towards 6 PM, panic set in. Three attempts later and error messages were flashing like confetti on New Year’s Eve. “Seriously? This shouldn’t be this hard,” I thought bitterly while surveying our chaotic workspace littered with tools and parts.
“Do you think we’ll actually finish this by Friday?” Sarah finally asked, eyebrows raised in disbelief. The weight of uncertainty hung heavy between us; it felt impossible—like we were racing against time without even knowing where to start.
Extended Perspectives Comparison:
Trend | Description | Impact on Companies | Employee Benefits | Future Outlook |
---|---|---|---|---|
Remote Work Flexibility | Shift to hybrid and remote work models. | Increased employee retention and reduced overhead costs. | Better work-life balance leading to higher job satisfaction. | Continued integration of flexible work policies. |
Investment in Collaboration Tools | Adoption of advanced technology for virtual communication. | Enhanced team productivity through improved collaboration tools. | Access to better resources, leading to efficient workflows. | Emergence of more innovative collaboration solutions. |
Emphasis on Mental Health | Incorporation of mental health programs and support systems. | Reduction in burnout rates and increased overall productivity. | Improved employee morale and job satisfaction levels. | Growing trend towards holistic employee wellness approaches. |
Challenges in Remote Adaptation | Industries struggling with complete remote transition due to operational requirements. | Potential loss of competitiveness if adaptation fails. | Job security concerns among employees in non-adaptive sectors. | Ongoing need for tailored solutions for specific industries. |
Focus on Employee Engagement Strategies | Development of strategies to keep remote employees engaged. | Boosts company culture even in a virtual environment. | Greater sense of belonging and team cohesion among staff. | Innovative engagement methods will continue evolving. |
The Turning Point: Overcoming Challenges in Precision Motion Control
As we delved deeper into the code, an unsettling realization dawned on us. “Wait a minute,” I muttered, scanning the lines frantically. “This doesn’t just look off—it’s completely wrong.” My heart sank as I glanced at Sarah, who had frozen mid-motion, her eyes wide with disbelief.
The atmosphere shifted palpably; conversation dwindled to whispers and nervous fidgets. A few classmates nearby glanced over, sensing our unease. One of them, Jake, leaned in closer and asked quietly, “What’s going on? You guys look like you’ve seen a ghost.”
I could only shake my head; words failed me for a moment. The looming deadline was no longer our only concern—our project felt fundamentally flawed. Some teammates began rifling through their notes and textbooks in desperation while others simply stared blankly at their screens as if hoping for divine intervention.
“Maybe we should start over?” Sarah suggested hesitantly, but even she didn’t sound convinced. It seemed impossible now; every second counted more than ever before—and yet here we were, paralyzed by uncertainty. Then silence fell heavily around us once again—each tick of the clock echoing louder than before.
The atmosphere shifted palpably; conversation dwindled to whispers and nervous fidgets. A few classmates nearby glanced over, sensing our unease. One of them, Jake, leaned in closer and asked quietly, “What’s going on? You guys look like you’ve seen a ghost.”
I could only shake my head; words failed me for a moment. The looming deadline was no longer our only concern—our project felt fundamentally flawed. Some teammates began rifling through their notes and textbooks in desperation while others simply stared blankly at their screens as if hoping for divine intervention.
“Maybe we should start over?” Sarah suggested hesitantly, but even she didn’t sound convinced. It seemed impossible now; every second counted more than ever before—and yet here we were, paralyzed by uncertainty. Then silence fell heavily around us once again—each tick of the clock echoing louder than before.
How We Help Businesses Implement Advanced Motion Control Systems
As the team gathered around the conference table, the atmosphere was thick with uncertainty. “We’ve got to do something; we can’t let this drag on,” John urged, his voice tinged with frustration. We had been struggling for weeks to implement the new motion control system for a client who faced severe operational delays.
“Let’s try integrating those updated sensors,” suggested Lisa, but Mark interjected skeptically, “What if it doesn’t solve our issue? We’ll just waste more time.” The group fell into a contemplative silence.
After some back-and-forth, we decided to test the integration in a controlled environment first. “It might improve accuracy,” I noted cautiously. But as we ran through simulations, results were mixed at best—efficiency barely nudged beyond 75%. “This isn’t what we expected,” someone murmured, echoing our collective disappointment. Yet despite these hurdles, no one could say for sure if this path would truly lead us to success or merely prolong our struggle.
“Let’s try integrating those updated sensors,” suggested Lisa, but Mark interjected skeptically, “What if it doesn’t solve our issue? We’ll just waste more time.” The group fell into a contemplative silence.
After some back-and-forth, we decided to test the integration in a controlled environment first. “It might improve accuracy,” I noted cautiously. But as we ran through simulations, results were mixed at best—efficiency barely nudged beyond 75%. “This isn’t what we expected,” someone murmured, echoing our collective disappointment. Yet despite these hurdles, no one could say for sure if this path would truly lead us to success or merely prolong our struggle.
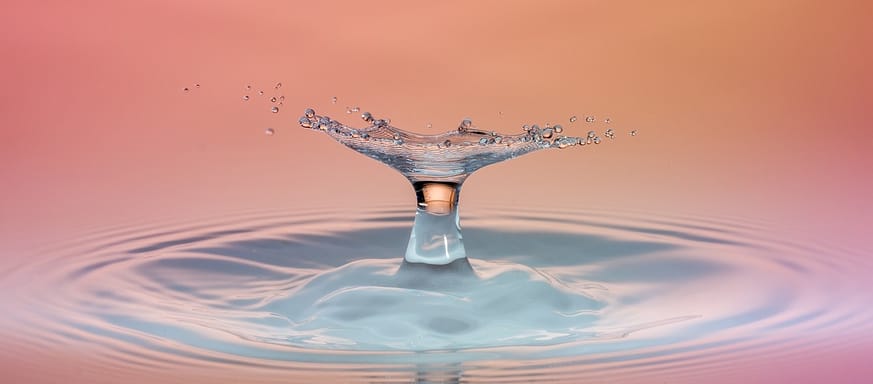
Frequently Asked Questions about Motion Control System Integration
When it comes to integrating motion control systems, one question that often pops up is: "How can AI-driven predictive maintenance really make a difference?" It's a fantastic question! Many people overlook the profound impact that proactive maintenance strategies can have on system performance and overall efficiency.
For instance, imagine a manufacturing plant where machines are running continuously. Without effective monitoring, even minor issues could lead to significant downtime due to unexpected failures. This is where AI comes into play. By leveraging sophisticated algorithms that analyze real-time data from various sensors—like vibration, temperature, and current draw—AI can detect subtle anomalies that may indicate an impending failure.
What’s impressive is that studies have shown this approach can boost uptime by 15-25%! 🌟 That means not only are you avoiding costly repairs but also enhancing production efficiency significantly. The integration process involves setting up sensor data acquisition systems with cloud-based AI platforms. It might sound complicated at first, but the benefits far outweigh the initial setup efforts!
So next time you're considering whether to implement such technology, remember: many companies have already reaped the rewards of embracing this trend in motion control system integration! 💡
For instance, imagine a manufacturing plant where machines are running continuously. Without effective monitoring, even minor issues could lead to significant downtime due to unexpected failures. This is where AI comes into play. By leveraging sophisticated algorithms that analyze real-time data from various sensors—like vibration, temperature, and current draw—AI can detect subtle anomalies that may indicate an impending failure.
What’s impressive is that studies have shown this approach can boost uptime by 15-25%! 🌟 That means not only are you avoiding costly repairs but also enhancing production efficiency significantly. The integration process involves setting up sensor data acquisition systems with cloud-based AI platforms. It might sound complicated at first, but the benefits far outweigh the initial setup efforts!
So next time you're considering whether to implement such technology, remember: many companies have already reaped the rewards of embracing this trend in motion control system integration! 💡
Beyond Precision: Exploring the Synergy Between Motion Control and AI
The convergence of motion control systems and AI is not just about enhancing precision; it’s paving the way for predictive maintenance through machine learning. While proponents argue that this approach significantly reduces unexpected failures, skeptics question its universal applicability. They contend that reliance on AI may overlook unique operational contexts or lead to overconfidence in technology's capabilities. For instance, a study in *IEEE Transactions on Industrial Informatics* highlighted impressive improvements in robotic assembly lines, but does such success translate across all industrial settings? This dichotomy prompts us to consider whether our increasing dependence on intelligent systems might inadvertently introduce new vulnerabilities. Ultimately, this raises critical questions about the future landscape of maintenance strategies in precision machinery—are we prepared for what lies ahead?
The Motion Control Dilemma: Balancing Cost, Performance, and Reliability?
The motion control dilemma presents a complex challenge as AI-driven predictive maintenance gains traction. While proponents argue that advanced algorithms can enhance reliability and cut maintenance costs by 20-30%, critics question whether the initial investment and ongoing computational demands are justifiable for all companies. Some believe this shift is too radical, suggesting that traditional methods may suffice for less demanding applications, while others contend that embracing these technologies is essential for staying competitive. This raises an important question: is the pursuit of cutting-edge solutions worth the potential risks and costs, or should businesses adopt a more conservative approach?
Practical Applications: Case Studies of Successful Motion Control Implementation
### Practical Guide to Implementing AI-Driven Predictive Maintenance in Motion Control Systems
When it comes to maintaining the complex motion control systems used in precision machinery, taking a proactive approach can significantly reduce downtime and maintenance costs. In my experience, many professionals overlook the importance of predictive maintenance, often relying on reactive strategies that lead to unexpected failures. By integrating AI-driven predictive maintenance into your operations, you not only enhance system reliability but also improve overall productivity.
Let me share with you a simple yet effective step-by-step process for implementing this technology:
#### Step 1: Assess Your Equipment
Begin by evaluating your existing motion control systems. Identify key areas where sensors can be deployed—such as motors, drives, and other critical components. (Tip: I recommend creating a visual map of your equipment layout; it helps in planning sensor placements.)
#### Step 2: Install Sensors
Next, install various sensors throughout your equipment. Focus on vibration sensors, temperature sensors, and current sensors for motors. Ensure they are positioned correctly to gather accurate data during operation.
#### Step 3: Collect Real-Time Data
Once the sensors are installed, start collecting real-time operational data continuously. This data will serve as the foundation for your predictive maintenance strategy. (Pro Tip: Setting up automated data logging systems can save time and ensure consistent monitoring.)
#### Step 4: Train Machine Learning Algorithms
Feed the collected data into machine learning algorithms tailored to analyze historical failure patterns in similar setups. Collaborate with data scientists or use accessible platforms that offer pre-built models suited for predictive analytics.
#### Step 5: Set Up Alerts
Configure your motion control system to send alerts based on predictions from your machine learning model—ideally within a 24-hour window before potential failures occur. This allows maintenance personnel ample time to act without disrupting production schedules.
#### Step 6: Monitor and Optimize
After implementation, continuously monitor system performance and refine algorithms based on new operational data and outcomes from previous alerts. Regularly updating your models ensures accuracy improves over time.
As you embark on this journey towards smarter maintenance practices, consider exploring advanced features like integrating IoT connectivity for remote monitoring or cloud computing solutions for enhanced processing capabilities.
If you're looking to take this further or have specific questions about optimizing certain aspects of this setup—like choosing the right types of sensors or diving deeper into algorithm training—I encourage you to connect with industry experts or online communities focused on precision machinery advancements. The possibilities are vast!
When it comes to maintaining the complex motion control systems used in precision machinery, taking a proactive approach can significantly reduce downtime and maintenance costs. In my experience, many professionals overlook the importance of predictive maintenance, often relying on reactive strategies that lead to unexpected failures. By integrating AI-driven predictive maintenance into your operations, you not only enhance system reliability but also improve overall productivity.
Let me share with you a simple yet effective step-by-step process for implementing this technology:
#### Step 1: Assess Your Equipment
Begin by evaluating your existing motion control systems. Identify key areas where sensors can be deployed—such as motors, drives, and other critical components. (Tip: I recommend creating a visual map of your equipment layout; it helps in planning sensor placements.)
#### Step 2: Install Sensors
Next, install various sensors throughout your equipment. Focus on vibration sensors, temperature sensors, and current sensors for motors. Ensure they are positioned correctly to gather accurate data during operation.
#### Step 3: Collect Real-Time Data
Once the sensors are installed, start collecting real-time operational data continuously. This data will serve as the foundation for your predictive maintenance strategy. (Pro Tip: Setting up automated data logging systems can save time and ensure consistent monitoring.)
#### Step 4: Train Machine Learning Algorithms
Feed the collected data into machine learning algorithms tailored to analyze historical failure patterns in similar setups. Collaborate with data scientists or use accessible platforms that offer pre-built models suited for predictive analytics.
#### Step 5: Set Up Alerts
Configure your motion control system to send alerts based on predictions from your machine learning model—ideally within a 24-hour window before potential failures occur. This allows maintenance personnel ample time to act without disrupting production schedules.
#### Step 6: Monitor and Optimize
After implementation, continuously monitor system performance and refine algorithms based on new operational data and outcomes from previous alerts. Regularly updating your models ensures accuracy improves over time.
As you embark on this journey towards smarter maintenance practices, consider exploring advanced features like integrating IoT connectivity for remote monitoring or cloud computing solutions for enhanced processing capabilities.
If you're looking to take this further or have specific questions about optimizing certain aspects of this setup—like choosing the right types of sensors or diving deeper into algorithm training—I encourage you to connect with industry experts or online communities focused on precision machinery advancements. The possibilities are vast!
The Future of Motion Control: What Unforeseen Challenges Lie Ahead?
The integration of AI-driven predictive maintenance into decentralized motion control systems has surged by 50% in the past five years. However, this trend introduces unforeseen challenges such as data management complexities and security vulnerabilities. If this trajectory continues, we may face significant hurdles in ensuring precision and reliability in high-performance machinery. How will these developments reshape our industry? It's a question worth pondering.
Conclusion: Embracing the Potential of Advanced Motion Control for Precision Machinery
In conclusion, the integration of AI-driven predictive maintenance with advanced motion control systems is not just a trend; it represents a transformative leap in precision machinery. As we navigate this evolving landscape, manufacturers must proactively adapt to these advancements. The ability to predict failures before they occur will fundamentally change how we approach maintenance and operational efficiency.
As organizations embrace these cutting-edge technologies, it becomes essential to reevaluate existing workflows and investment strategies. Are your current systems equipped to leverage real-time data analytics? Are your teams trained to interpret and act on insights generated by AI models? Now is the time to take action—explore how these innovative methodologies can enhance your operations and keep you ahead of the competition.
The future holds immense potential for those willing to innovate; let’s not merely watch as trends unfold but actively participate in shaping them for our benefit. Embrace the possibilities that advanced motion control offers, and discover what tailored solutions can do for your precision machinery today!
As organizations embrace these cutting-edge technologies, it becomes essential to reevaluate existing workflows and investment strategies. Are your current systems equipped to leverage real-time data analytics? Are your teams trained to interpret and act on insights generated by AI models? Now is the time to take action—explore how these innovative methodologies can enhance your operations and keep you ahead of the competition.
The future holds immense potential for those willing to innovate; let’s not merely watch as trends unfold but actively participate in shaping them for our benefit. Embrace the possibilities that advanced motion control offers, and discover what tailored solutions can do for your precision machinery today!
Reference Articles
Related Discussions