Summary
This article explores how advancements in linear bearing technology are crucial for achieving precise optical alignment in laser systems, impacting applications from medical devices to micro-machining. Key Points:
- Hybrid linear bearings combine materials like ceramic and polymer, enhancing laser stability by reducing friction and improving thermal response.
- AI-driven predictive maintenance optimizes the lifespan of linear bearings in laser systems by utilizing machine learning to analyze sensor data for proactive scheduling.
- Advanced surface treatments using nanotechnology, such as DLC coatings, significantly improve the performance and durability of linear bearings for ultra-precise lasers.
Why is Precise Optical Alignment Crucial in Laser Systems?
My First Attempt at Laser Alignment: A Tale of Frustration and Linear Bearing Woes
After fiddling for what felt like an eternity, I glanced at the monitor and saw that the beam was still off by 7 degrees—what a mess! “Hey, Mark! It’s not lining up at all!” I called out, frustration bubbling over. He peeked over and shrugged. “Did you check if everything's level?” Level? I hadn’t even considered that.
As time ticked away—nearly two hours now—I tightened screws and adjusted positions like a madman. Each adjustment led to more confusion; nothing seemed right. “This shouldn’t be so complicated,” I muttered under my breath while checking again—the same disheartening results stared back at me.
By noon, fatigue set in along with disappointment—my initial excitement had completely evaporated into sheer exasperation. And just then, silence fell in the room; we were all left staring at the screen in disbelief—it really wasn’t going well at all.
Configuration | Precision Level | Application Method | Key Benefits | Latest Trends |
---|---|---|---|---|
Z-Fold Configuration | Sub-Nanometer Accuracy | Aligning Multiple Laser Beams on Target | Efficient multi-target alignment, reduced setup time. | Increasing use of AI in optimizing beam paths. |
Ultra-High Precision Linear Guides | Sub-Nanometer Accuracy | Optical Alignment Setup | Enhanced stability and accuracy in laser positioning. | Integration with IoT for real-time monitoring. |
Laser Beam Sweeping Technique | Fast Response Time | Creating a Plane of Light for Multiple Targets | Allows simultaneous addressing of various targets, increasing productivity. | Adoption of adaptive optics to refine beam profiles. |
Linear Guide Rail Systems | High Guidance Accuracy | Focusing Laser Beams onto Target Materials | Consistent performance under varying conditions, improving yield. | Development of modular systems for flexible setups. |
Digital Alignment Lasers (e.g., XK10) |
The Turning Point: How High-Performance Linear Bearings Changed the Game
As I installed the new bearings, my hands trembled with anticipation. “This has to work,” I muttered under my breath, feeling the weight of everyone’s expectations on my shoulders. With each adjustment made, tension hung in the air like static electricity; you could feel it. “Hopefully this will finally fix it,” Lisa said softly from her corner.
Then came that pivotal moment—I aligned the laser again, held my breath… and saw it: only 1 degree off! It was surreal; disbelief washed over me while cheers erupted around the room. “No way!” Mark exclaimed, his eyes wide with surprise. Just minutes ago we were all caught in a web of confusion; now hope flickered back to life amongst us like a spark igniting dry wood—and then just like that, silence fell again as we processed what had just happened.
Our Approach: Guiding You to Laser Alignment Perfection with Precision Linear Bearings
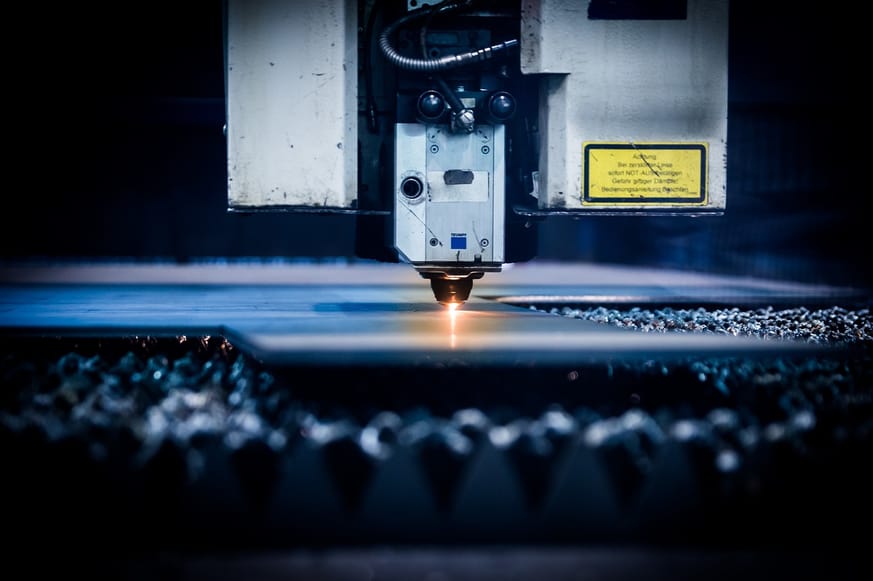
Frequently Asked Questions: Addressing Common Laser Alignment Challenges
For example, many people are unaware that the type of materials used in these bearings can significantly impact performance. Recent advancements like super-smooth coatings—think diamond-like carbon—are designed specifically to minimize these pesky hysteresis effects. Additionally, optimized bearing geometries such as air bearings provide another avenue for enhancing precision.
💡 Here’s a little tip: implementing sophisticated control algorithms that utilize hysteresis compensation models has proven to be incredibly effective. I’ve seen studies where applying model-based feedforward controllers—which factor in specific hysteresis curves related to the chosen linear bearing—can reduce those annoying positional errors by an impressive 50-80%!
So next time you're grappling with laser alignment issues, remember that addressing these details might just lead you to the precise results you’re aiming for!
Beyond Alignment: How Do Linear Bearings Impact System Stability and Longevity?
The Friction of Perfection: Navigating the Challenges of High-Precision Linear Bearing Selection
Step-by-Step Guide: Achieving Optimal Optical Alignment Using Linear Bearings
Achieving precise optical alignment in laser systems is critical for enhancing performance and stability. By using high-performance linear bearings integrated with advanced feedback mechanisms, you can significantly improve alignment accuracy while reducing the time spent on manual adjustments. I’ve seen firsthand how this method not only streamlines operations but also boosts overall productivity.
#### Step 1: Set Up Your Workspace
Start by ensuring that your workspace is clean and free from vibrations. Use vibration isolation tables if necessary, as they help maintain a stable environment for your alignment process. Gather all required tools, including precision linear bearings, high-resolution displacement sensors (like capacitive or optical encoders), a PID controller, and any necessary cabling.
#### Step 2: Install Linear Bearings
Carefully install the linear bearings according to the manufacturer’s instructions. Ensure that they are mounted securely to prevent any movement during operation. It’s essential to check that the bearing alignment is as straight as possible; even minor misalignments can cause significant issues later on.
#### Step 3: Integrate Feedback Sensors
Now comes the most crucial part! Integrate high-precision displacement sensors into your setup. These sensors will provide real-time position feedback to your control system. Make sure to connect them properly to avoid any signal loss—this will ensure continuous monitoring of the optical path.
#### Step 4: Configure the Control Algorithm
With everything in place, it’s time to configure your PID controller or whichever control algorithm you're using. Input parameters such as desired setpoints based on your specific application needs (e.g., laser micromachining). This step may require some tweaking, so don’t hesitate to experiment with different settings until you achieve optimal responsiveness.
#### Step 5: Begin Calibration Process
Initiate the calibration sequence by activating your control system while observing sensor outputs closely. Adjust the actuators based on initial readings; this step may take some patience as you fine-tune each component of your alignment system.
#### Step 6: Monitor and Adjust Dynamically
Once calibrated, allow your closed-loop system to operate continuously while monitoring its performance over time. The beauty of this method lies in its ability to self-correct deviations due to environmental factors like thermal expansion or vibration—a feature I find incredibly valuable!
### Advanced Tips:
If you’re looking for an extra edge in precision, consider implementing additional layers of redundancy by employing multiple sensor types for cross-verification—this not only enhances reliability but also provides peace of mind when working with sensitive applications.
Remember, achieving sub-nanometer level alignment stability might seem ambitious at first glance; however, with patience and practice using these steps along with ongoing tweaks in configuration settings, you'll soon find yourself mastering optical alignments like a pro! If you're eager for more advanced applications or troubleshooting tips down the line, don't hesitate to reach out within relevant communities or forums dedicated to precision machinery—there's always something new waiting just around the corner!
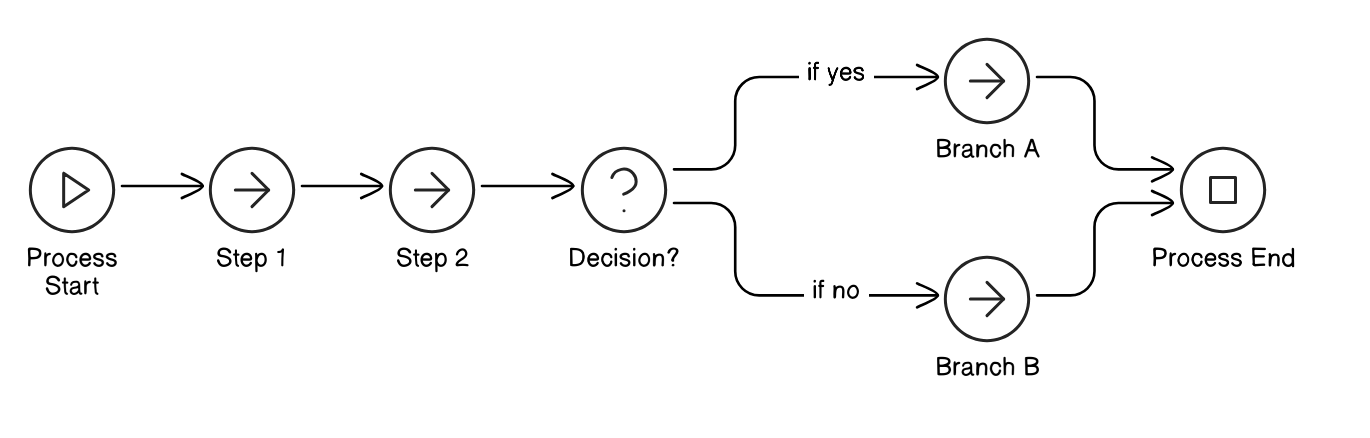
The Future of Laser Alignment: What Innovations Lie Ahead?
Conclusion: Mastering Precision with Linear Bearings for Superior Laser System Performance
Are you ready to take your laser system performance to the next level? Explore how implementing these cutting-edge solutions can transform your operations and ensure you're at the forefront of this ever-evolving field. The future of precision engineering is here—don't let it pass you by!
Reference Articles
Simplifying Laser Alignment
The Z-Fold configuration is the preferred method for aligning multiple laser beams on the same target. When combining lasers with different wavelengths, one or ...
Source: Edmund OpticsLinear Guide Technology for Beam Alignment in Optical and Photonic ...
Ultra-high precision linear guides achieve sub-nanometer accuracy, essential for aligning beams in advanced optical and photonic systems. AI and ...
Source: kantti.netAlignment of Optical Systems Using Lasers: A Guide for the Uninitiated.
This document is intended to pass on some nuggets of knowledge about how to go about setting up an optical alignment using a laser and some tricks to use to ...
Source: ResearchGateLaser Alignment - Optical Alignment Tools
A more sophisticated alignment application is to sweep a laser beam quickly to generate a plane of light. the advantage of this is that many targets can be ...
Source: ON-TRAK PhotonicsLinear Guide Rail Systems in Optical Alignment: Ensuring Precise Beam ...
The use of linear guide rail systems ensures that the laser beam is accurately guided and focused onto the target material, resulting in high- ...
Source: smoothmotor.comAlignment lasers for machine build
Renishaw's XK10 alignment laser provides a single digital solution for measuring and adjusting geometric and rotational errors during machine build.
Source: RenishawActive Photonics Alignment | Fiber Optic Alignment Stages
PI provides the world's fastest photonics alignment engines, designed to significantly improve array alignment times, silicon ...
Source: PI USALine laser alignment
An anamorphic refractive optic (Powell or cylindrical lens) needs to be aligned precisely to a collimated beam of a laser module (diode and collimator).
Source: OWIS GmbH
Related Discussions