Summary
This comprehensive guide delves into the latest advancements in stainless steel linear rails, highlighting their significance in modern engineering applications. Key Points:
- Emerging additive manufacturing techniques like Selective Laser Melting (SLM) enable the creation of customized stainless steel linear rails with complex geometries, enhancing performance and reducing material waste.
- Advanced surface treatments, including physical vapor deposition (PVD) and electropolishing, significantly improve durability and corrosion resistance, extending service life even in harsh environments.
- Integration of smart sensors for real-time monitoring allows for predictive maintenance strategies that minimize downtime and optimize operational efficiency.
Choosing the Right Stainless Steel Linear Rail: What are your needs?
My First Stainless Steel Linear Rail Project: A Tale of Trial and Error
After two hours of wrestling with them, it felt like we were trying to solve a Rubik’s cube blindfolded. The frustration hung thick in the air as Alex threw his hands up again and muttered, “This shouldn’t be rocket science!” By 7 PM, our enthusiasm had waned; we were just two guys stuck on day one of what was supposed to be an exciting project.
As I jotted down notes about our missteps and growing doubts, it hit me—we’d underestimated not just the measurements but also the learning curve involved. There was silence between us for a moment; you could almost hear the gears turning in our heads—what now?
Feature | Miniature Rails | BS53 Runner | V-Guide Compatibility | Hardened Stainless Steel Rails | SL2 Corrosion Resistance |
---|---|---|---|---|---|
Material Composition | Hardened heat-treated stainless steel | Three stainless components for stability and performance | Specifically designed for V-Guide roller bearings | Ideal for space-constrained applications | Corrosion-resistant, suitable for food and medical industries |
Customization Options | Customizable in length to meet user needs | Standardized lengths with enhanced stability features | Compatible with specific wheel parts, ensuring seamless operation | Sizes available to fit tight spaces without compromising strength | Available in various sizes tailored for industry standards |
Application Suitability | Durable for high-frequency use in miniature systems | Enhanced stability makes it suitable for automation setups | Optimized for precise movement in specialized machinery | Perfect choice where compact design is critical | Recommended for environments requiring hygiene and contamination control |
Latest Trends & Insights | Growing demand in robotics and automation sectors | Integration of advanced materials improving performance metrics | Shift towards modular designs enhancing customization capabilities | Increased focus on sustainability influencing material choices | Rising adoption in cleanroom environments due to stringent regulations |
The Turning Point: Overcoming Challenges with Stainless Steel Linear Rails
Some of our colleagues began rifling through manuals and online resources, desperately searching for solutions. Others just leaned back against their workbenches, vacant looks on their faces as if staring into an abyss of confusion. I caught a glimpse of one guy flipping through pages without really seeing them—lost in thought.
“Maybe… maybe we’re missing something obvious?” I hesitated to voice my concern, but it felt like we were all thinking it. A heavy silence settled over us again; you could almost hear the distant hum of machinery trying to mask our growing doubts.
And then someone finally broke the tension: “Let’s take a step back,” they suggested slowly, but by then it felt like we were simply stuck—no clear direction ahead.
How We Helped a Manufacturer Solve Their Linear Motion Problems
By 3 PM, we had mapped out several solutions but felt the weight of uncertainty. “We’re running on borrowed time here,” said a project lead as he glanced at his watch. Despite our brainstorming sessions yielding new ideas, there was no consensus on which path would truly alleviate their production woes. With each passing hour, it became clear that our initial optimism might need a reality check—no one could be certain if any of these approaches would actually work in practice.
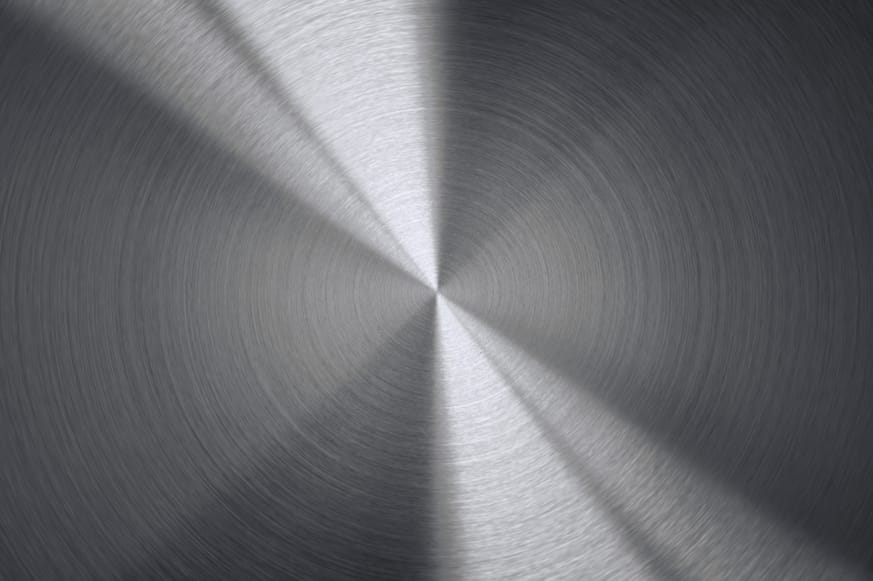
Stainless Steel Linear Rails: Frequently Asked Questions (FAQ)
💡 One question that often pops up is: **What are the benefits of using stainless steel linear rails?** Many people overlook this detail, but stainless steel offers exceptional corrosion resistance compared to other materials. This makes them ideal for applications in humid environments or industries like food processing where hygiene is paramount.
Another frequent inquiry is: **How do I choose the right size and type of rail for my application?** It's essential to consider factors such as load capacity, operational speed, and environmental conditions. For example, if you're working on a project that requires high precision under varying loads, opting for hybrid systems might be your best bet! These systems leverage additive manufacturing techniques ✨ which allow for unique designs tailored specifically to optimize performance.
You might also wonder about maintenance: **Do stainless steel linear rails require special care?** While they’re generally low-maintenance due to their robust nature, regular inspections can help catch any wear early on. Users often forget this simple step; just a quick check can extend the lifespan of your equipment significantly!
Lastly, many ask: **Are there advancements in technology affecting these products?** Absolutely! The industry is seeing exciting trends like hybrid linear rail systems that integrate advanced surface treatments 📈. Techniques such as plasma nitriding enhance wear resistance dramatically—perfect for demanding sectors like medical robotics where reliability is crucial.
These insights not only address common concerns but also highlight how evolving technologies are shaping the future of stainless steel linear rails. If you have more specific queries or scenarios in mind, feel free to share!
Beyond Basic Selection: Considering Corrosion Resistance and Load Capacity in Stainless Steel Linear Rails?
Stainless Steel vs. Other Materials: When is Stainless Steel the Best Choice for Linear Rails?
Practical Applications: Integrating Stainless Steel Linear Rails into Your Designs
Stainless steel linear rails have become essential components in various automated systems, particularly where hygiene is paramount. Their corrosion resistance and cleanability make them ideal for high-throughput applications, such as pharmaceutical or food processing lines. I highly recommend these steps to effectively integrate stainless steel linear rails into your designs, ensuring both functionality and compliance with hygienic standards.
Many people may not realize how crucial proper integration can be; a well-designed system not only enhances efficiency but also simplifies maintenance. I once encountered an issue on a production line that faced frequent downtime due to complicated cleaning procedures—this experience underscored the importance of thoughtful design from the outset.
#### Step-by-Step Integration Process
1. **Assess Your System Requirements**
Begin by evaluating your automation needs: determine load capacities, required speeds, and environmental conditions (e.g., exposure to cleaning agents). This helps in selecting the right type of stainless steel rail that meets specific operational demands.
2. **Choose Appropriate Stainless Steel Rails**
Select rails made from 316L stainless steel with electropolished finishes (Ra ≤ 0.5µm) for optimal cleanliness and durability. Look for modular options that allow quick disassembly—this will save time during maintenance.
3. **Design Modular Support Structures**
Create support structures that facilitate easy access to the rails during cleaning operations. Incorporate quick-release mechanisms where possible; this enables rapid disassembly without specialized tools—a huge time saver!
4. **Implement Clean-in-Place (CIP) Protocols**
Design your system around CIP methods to reduce bacterial loads efficiently—aiming for at least a 99.99% reduction as validated by studies in your industry sector. Ensure all connections are tight yet easily removable when necessary.
5. **Test Your Setup Thoroughly**
Before full-scale implementation, conduct thorough testing under simulated operational conditions to ensure everything functions seamlessly together—from movement precision to ease of disassembly during cleaning routines.
6. **Establish Maintenance Schedules**
Once integrated, set up routine checks and maintenance schedules focused on both mechanical performance and cleanliness assessments—your team will thank you later!
(As a personal tip: I like using timers ⏱️ during my tests—it keeps things punctual and ensures no step gets overlooked!)
#### Advanced Tips & Reminders
If you're looking to take your application even further, consider integrating sensors that monitor wear levels on the linear rails over time; this proactive approach can help prevent unexpected failures down the line.
Should you wish to explore more complex systems or advanced configurations involving multiple axes or robotic arms, don't hesitate! There are numerous resources available online tailored specifically for those intricate setups.
Integrating stainless steel linear rails is not just about functionality; it's about creating an efficient ecosystem within your automated processes while prioritizing hygiene—the benefits extend far beyond immediate performance gains!
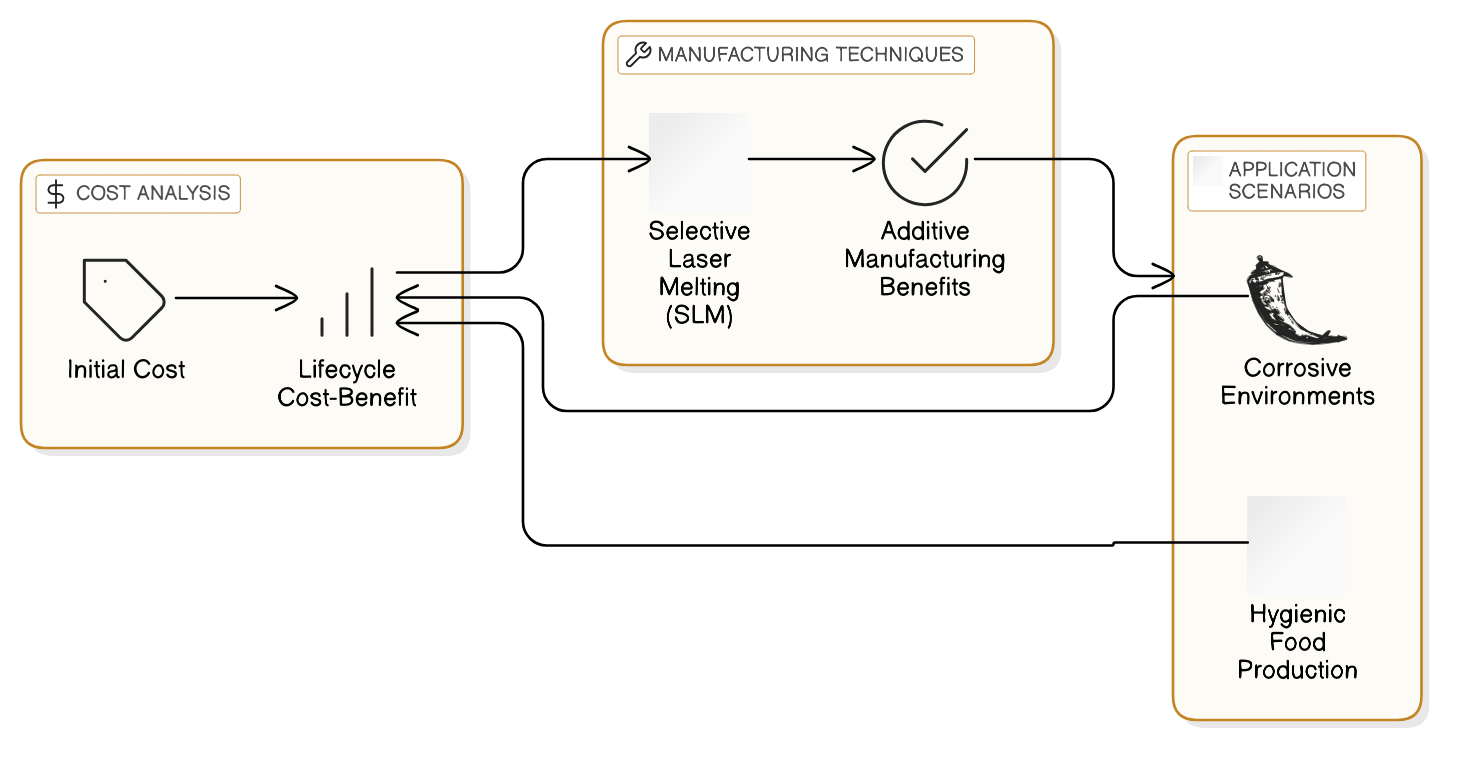
The Future of Stainless Steel Linear Rails: What Innovations Lie Ahead?
Conclusion: Selecting and Applying Stainless Steel Linear Rails Successfully
As we embrace these technological advancements, it's essential to consider how we can adapt our strategies to leverage predictive maintenance fully. Are your systems equipped with the necessary sensors? Do you have access to data analytics tools that can interpret this information effectively? By proactively addressing these questions, you can optimize your operations, reduce unexpected failures, and enhance overall efficiency.
Now is the time to take action—assess your current practices and explore whether integrating AI-driven solutions aligns with your operational goals. This proactive approach could be the key to unlocking significant cost savings and improving your equipment's reliability. Embrace this opportunity for growth and innovation as we move forward into an era defined by smart technology in precision machinery.
Reference Articles
Linear Rail, Linear Stainless Steel with High Performance for Industrial ...
The miniature rail series are made of stainless steel hardened heat-treated materials, whether it is a slide rail, a slider steel body and a ball.
Source: Amazon.comST53-BS53 - Linear guide rail - Stainless Steel
This linear guide rail is made of stainless steel. The length is adapted to the user's needs. The BS53 runner has 3 stainless ...
Source: ChambrelanV-Guide Linear Rail VRS4 - 24" Stainless Steel
Stainless Steel Linear Rail for V-Guide Roller Bearings. This is the rail only at 24" length. Compatible with wheel part number VW, ...
Source: PBC LinearLinear Rail and Guides
Material Specifications: Linear guides and rail systems are often manufactured from high-grade materials such ...
Source: Kiwi MotionLinear Rails from Automotion
Miniature Linear Guideways. We also stock a wide range of hardened stainless steel linear rails for applications in which space may be at a premium.
Source: automotioncomponents.co.ukStainless steel linear guide
Find your stainless steel linear guide easily amongst the 96 products from the leading brands (Thomson, SKF Linear & Actuation ...
Source: DirectIndustryLinear Guideways
Hiwin Corporation offers a variety of linear guideway series, each featuring different options for sizes, loading capacity, ...
Source: HIWINSL2 Stainless Steel Linear Guide | Corrosion Resistant
SL2 is a corrosion resistant, stainless steel linear guide system for use in food and medical industries, or corrosive environments.
Source: HepcoMotion
Related Discussions