Summary
This article explores Industry 4.0 technologies and their transformative impact on smart factories, emphasizing the importance of innovation for modern manufacturing. Key Points:
- Decentralized Autonomous Organizations (DAOs) enhance transparency and efficiency in manufacturing by leveraging blockchain technology, moving towards autonomous production systems.
- Integrating physics-based models with AI creates hybrid systems that improve predictive maintenance and process optimization in manufacturing.
- Digital twins in metaverse environments enable real-time collaborative design, significantly reducing product development cycles.
What is Industry 4.0 and Why Does It Matter
In today's fast-paced technological environment, Industry 4.0 is at the cutting edge, promising to transform manufacturing and various other sectors. This term refers to the ongoing automation and data exchange within manufacturing technologies, culminating in what many describe as a "smart factory." But what does Industry 4.0 truly encompass, and why is it critical?
Understanding Industry 4.0 involves recognizing its roots in previous industrial revolutions that have significantly altered economic and social frameworks. It emphasizes the integration of cyber-physical systems, which incorporate real-time data analytics and machine learning algorithms for predictive maintenance and efficiency gains. The Internet of Things (IoT) plays a vital role by connecting devices across manufacturing environments, enhancing operational interconnectivity.
Moreover, advanced sensors and AI-driven robotics are pivotal in fostering greater automation and flexibility within smart factories. These innovations collectively boost productivity and drive industry-wide advancements, making Industry 4.0 an essential focus for businesses aiming to stay competitive in this new era of industrial evolution.
A Look Back at the Previous Industrial Revolutions
As we progress through these revolutions, it’s important to note that steam power laid the groundwork for electrical energy in the Second Industrial Revolution. This evolution continued into automation with robotics during what is often referred to as the Third Industrial Revolution. Additionally, foundational materials such as iron and steel enabled mechanization while advanced composites and smart materials are shaping Industry 4.0 today. Understanding these elements provides a clearer picture of technological advancement throughout history and illustrates their impact on modern smart factories.
Key Element | Description | Impact on Industry 4.0 |
---|---|---|
Industry 4.0 Overview | Integration of automation and data exchange in manufacturing. | Transforms traditional factories into smart factories. |
Core Technologies | Includes IoT, AI, Big Data, Additive Manufacturing, Cloud Computing. | Enhances operational efficiency and responsiveness. |
IoT Role | Connects devices for real-time data collection and analysis. | Enables autonomous operations and proactive maintenance. |
Big Data Significance | Extracts insights from vast data sources for decision-making. | Optimizes production processes, reduces costs. |
AI Applications | Processes large datasets to enhance production efficiency. | Identifies patterns for predictive maintenance and security enhancement. |
Understanding the Seamless Integration of Digital and Physical Systems
What truly distinguishes Industry 4.0 are the core technologies propelling this transformation. These include real-time data analytics, IoT (Internet of Things) sensor technologies, and advanced robotics that enhance operational efficiency and responsiveness. Principles of cyber-physical systems (CPS) facilitate continuous monitoring and create feedback loops for improved decision-making.
Moreover, innovative materials such as smart polymers or nanomaterials contribute to system agility while interoperability standards ensure effective communication among diverse systems. The role of edge computing is also critical; it minimizes latency for faster decisions in smart factories—further defining the landscape of Industry 4.0 advancements.
Key Technologies Driving the Transformation in Manufacturing
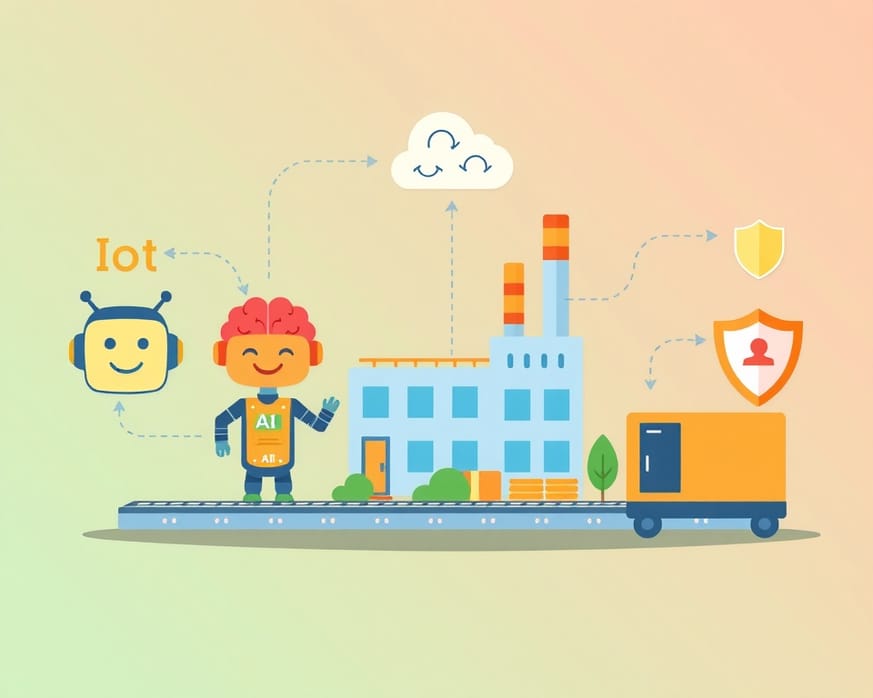
How IoT Enhances Automation and Operational Efficiency
This technological advancement is significantly aiding companies in increasing automation and improving agility while also enriching the customer experience. Moreover, specific IoT protocols like MQTT and CoAP play a crucial role in ensuring efficient communication between devices. The implementation of edge computing further mitigates latency issues and reduces bandwidth consumption by processing data closer to its source.
Security remains paramount; measures such as end-to-end encryption are essential for safeguarding sensitive information against cyber threats. Real-world applications demonstrate how integrating IoT solutions within smart factories leads to measurable improvements in both efficiency and productivity.
The Role of Big Data in Informed Decision Making
To enhance these capabilities, various data analytics techniques such as predictive analytics and machine learning are employed for real-time decision-making. The types of data collected include structured information—like numerical values—and unstructured formats—such as text or images—each sourced from IoT devices, sensors, and other technologies. By leveraging this rich pool of information, companies can significantly influence their operational efficiency and effectively manage risks.
Case studies from leading smart factories illustrate the tangible impact that big data has on performance optimization, showcasing how manufacturers utilize these insights to stay competitive in an increasingly complex landscape.
Exploring AI's Impact on Production Optimization and Security
To further illustrate AI's impact on production optimization and security enhancement, it’s important to consider how machine learning algorithms analyze historical data patterns to fine-tune production schedules dynamically. This real-time data integration helps reduce downtime by making necessary adjustments as situations evolve. Additionally, AI plays a crucial role in bolstering security through anomaly detection systems that identify potential threats or breaches within production environments. By examining successful case studies of these implementations, we can better understand the transformative effects of AI in various sectors.
The Benefits of Additive Manufacturing in Modern Production
Additive Manufacturing (AM), commonly known as 3D printing, allows for the creation of tailored, intricate parts by adding material layer by layer. As smart factories demand mass customization for their physical components, AM has emerged as a vital technology for producing bespoke products. Its capacity to craft sophisticated shapes with advanced properties using various materials makes it indispensable in modern manufacturing processes.
In addition to polymers, metals, and ceramics often utilized in additive manufacturing, each material offers unique characteristics suited to different applications across industries like aerospace and healthcare. This level of customization not only leads to innovative solutions but also minimizes waste and accelerates prototyping while ensuring high precision throughout production.
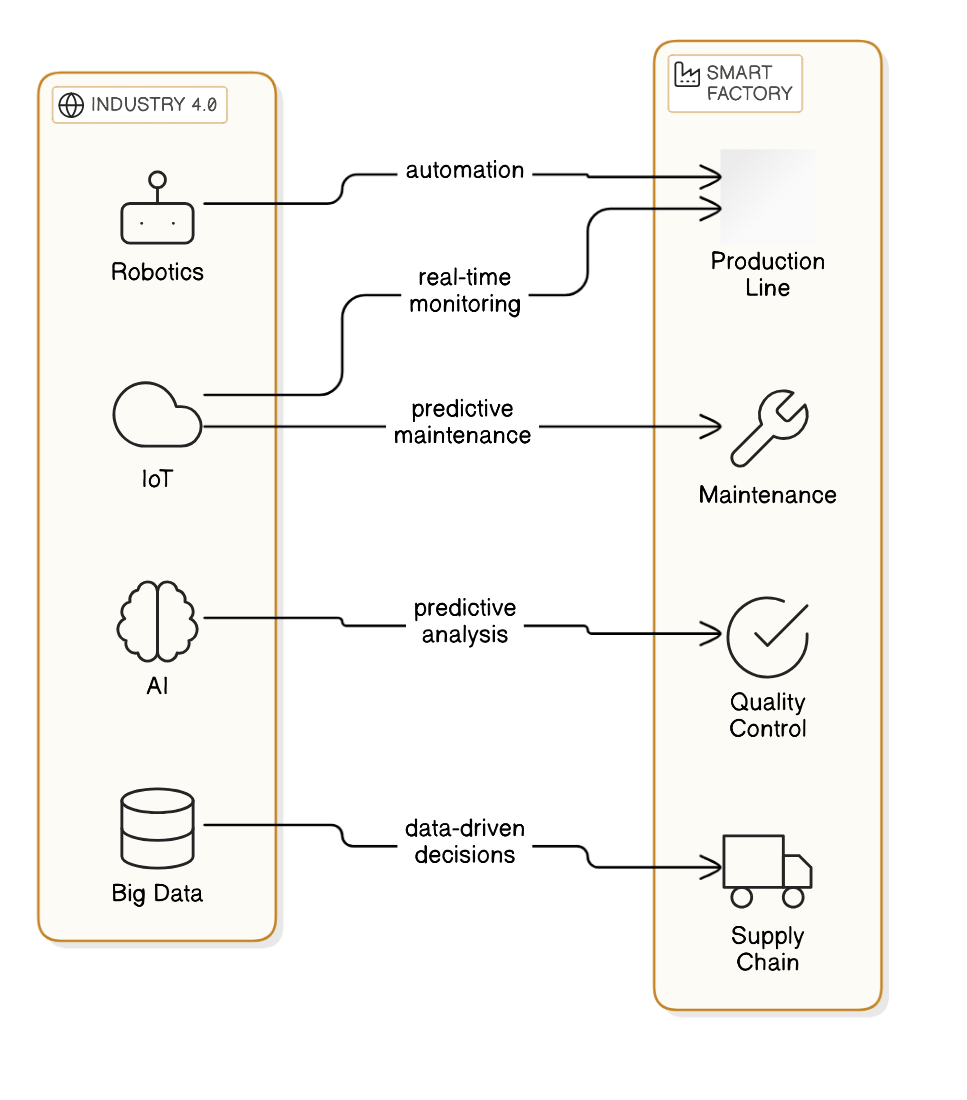
Cloud Computing: The Backbone of Smart Factories
Cloud computing serves as the backbone for processing and storing the vast amounts of data generated by smart factories. It provides on-demand access to computing resources such as physical and virtual servers, data storage, networking capabilities, development tools, software applications, and AI-driven analytics via the Internet. The pay-as-you-go pricing model allows businesses to efficiently scale their resources based on usage.
Moreover, cloud architectures like hybrid clouds or multi-cloud strategies optimize resource allocation while ensuring resilience and reliability. Integrating edge computing enhances real-time processing capabilities and facilitates low-latency communication between devices within smart factories. APIs play a vital role in enabling interoperability among various systems and devices, ensuring seamless data flow that bolsters operational efficiency in advanced manufacturing environments.
Addressing Challenges in Adopting Industry 4.0
Augmented Reality (AR) and Virtual Reality (VR) play vital roles in enhancing training, maintenance, and product design within Industry 4.0. AR enriches the physical world by overlaying digital artifacts—images, videos, or computer-generated images (CGI)—onto real environments using 3D models. In contrast, VR immerses users in a completely virtual environment through headsets and tracking technology. In practical settings, AR assists workers with real-time information for troubleshooting and maintenance tasks. On the other hand, VR enables simulations of factory layouts, product designs, or workflows that help teams optimize processes before actual implementation.
However, while transitioning to Industry 4.0 presents exciting opportunities for companies, it also brings significant challenges. As industries evolve into more intelligent and interconnected systems, they encounter hurdles including high initial investments and data security concerns.
Key challenges include:
1. **High Initial Investment**: Upgrading existing infrastructures to support Industry 4.0 can be prohibitively expensive for small- to medium-sized enterprises.
2. **Data Security and Privacy**: Increased connectivity heightens the risk of cyberattacks; therefore safeguarding sensitive data is crucial.
3. **Skill Gaps**: The shift requires a workforce adept at emerging technologies from previous advancements; specialized training is essential but may slow down adoption.
4. **Integration with Legacy Systems**: Many businesses still depend on outdated technologies that complicate seamless integration of modern solutions.
5. **Regulatory Compliance Issues**: Rapid technological advancements outpace government regulations regarding data sharing and privacy related to AI use in industries.
The transformation of the workforce in Industry 4.0 raises valid concerns about employment prospects due to automation's rise alongside emerging technologies historically linked with job displacement fears. Nevertheless, many experts assert that rather than leading to widespread job losses, Industry 4.0 will foster a shift in required skill sets and roles within the workforce.
While automation may replace specific manual jobs, it simultaneously creates new opportunities in areas like AI development and data analytics—cultivating demand for highly skilled laborers capable of navigating these advanced technologies effectively.
As industries embrace these innovations successfully allowing robots to collaborate closely with human workers enhances both productivity levels and workplace safety initiatives.
This transformation necessitates adaptability among employees who must commit to continuous learning to stay ahead amid rapid technological changes—a journey filled with both challenges yet abundant opportunities for growth within their fields.
In summary, as manufacturing undergoes this revolutionary change fueled by cutting-edge technologies like AI IoT big data organizations must remain agile while addressing potential obstacles directly leveraging core capabilities inherent within industry 4’s framework ultimately leading toward innovative interconnected responsive production landscapes ripe with possibilities ahead!
Reference Articles
What is Industry 4.0?
Industry 4.0, which is synonymous with smart manufacturing, is the realization of the digital transformation of the field, delivering real-time decision making.
Source: IBMIndustry 4.0: Smart Manufacturing Explained
Industry 4.0 is changing the way factories improve and distribute their products. Find out more about smart manufacturing here.
Source: Amper TechnologiesHow Industry 4.0 is Transforming Manufacturing
Industry 4.0 represents the convergence of digital technologies such as the Internet of Things (IoT), artificial intelligence (AI), big data analytics, cloud ...
Industry 4.0: The Future of Manufacturing
Industry 4.0 allows for smart manufacturing and the creation of intelligent factories. It aims to enhance productivity, efficiency, and flexibility.
Source: SAPUnderstanding the adoption of Industry 4.0 technologies in ...
This paper explores how Industry 4.0 technologies help create a sustainable environment in manufacturing and other industries.
Source: ScienceDirect.comUnderstanding Industry 4.0: Revolutionizing Modern ...
Thecore idea of Industry 4.0 is the creation of smart factories where machines and devices interact, share information, and make decisions autonomously. The ...
Source: Verizon
Related Discussions