Summary
This article explores the transformative impact of smart factories on modern manufacturing, emphasizing their significance in enhancing productivity and sustainability. Key Points:
- The integration of AI and digital twins enhances predictive maintenance by proactively identifying equipment failures, significantly reducing downtime.
- Adopting Zero Trust architecture and blockchain technology is essential for securing smart factories against cyber threats, ensuring only authorized access to sensitive data.
- AI-driven autonomous decision-making optimizes production schedules and resource allocation in real-time, improving efficiency and responsiveness.
What Is a Smart Factory
Picture a manufacturing setting where machines not only communicate with one another but also self-diagnose their maintenance requirements. These systems can automatically modify production schedules and allocate resources in response to shifting demands. In essence, a smart factory is driven by real-time data and predictive analytics that inform decision-making processes—eliminating uncertainty while significantly enhancing operational efficiency.
By harnessing cutting-edge digital technologies such as the Industrial Internet of Things (IIoT), big data analytics, robotics, and cloud computing capabilities, smart factories are redefining traditional manufacturing paradigms. Additionally, concepts like Cyber-Physical Systems (CPS) play a crucial role in enabling seamless automation and efficient data exchange within these environments.
Moreover, advanced materials including intelligent sensors and actuators facilitate real-time monitoring which supports adaptive manufacturing practices. Factors like scalability across various functions, interoperability between distinct systems, energy efficiency benchmarks, and cloud-based analytical tools further empower decision-making processes in these modern facilities. Ultimately, all these elements contribute to a more comprehensive understanding of how smart factories operate and their significance within contemporary manufacturing landscapes.
Key Components of a Smart Factory
### 1. Industrial IoT
At the heart of a smart factory lies the Industrial Internet of Things (IIoT). This framework relies on an extensive network of sensors, machines, and various devices that are interconnected. These devices consistently gather and share data, allowing for real-time oversight and management of manufacturing processes. Such connectivity offers remarkable transparency across all facets of the factory—from supply chain operations to production lines—enabling more informed decision-making. Moreover, IIoT devices can communicate directly with one another, facilitating machine-to-machine (M2M) interactions. This capability means that machines can autonomously adapt to dynamic conditions in their environment, thereby boosting efficiency while minimizing downtime. By harnessing the power of IIoT, smart factories can reach levels of automation and self-regulation that were once thought impossible.
### 2. Big Data and Analytics
In a smart factory setting, vast amounts of data are produced continuously. This is where big data technologies and analytics come into play—they enable the collection, storage, and analysis of this information to transform raw data into valuable insights. For example, predictive analytics can uncover patterns within the data that allow for proactive maintenance measures to be taken before equipment failures occur. Similarly, prescriptive analytics can provide actionable recommendations based on current data trends, enhancing decision-making processes and streamlining production workflows.
To further enhance these capabilities, integrating advanced sensors made from durable materials—such as stainless steel or specialized polymers—can withstand harsh industrial environments while ensuring accurate data collection. Additionally, incorporating artificial intelligence algorithms not only improves predictive maintenance strategies but also optimizes production schedules based on real-time analytics to reduce any potential downtime effectively. With robust cybersecurity measures in place to safeguard sensitive information and maintain seamless communication between components, smart factories are well-equipped to thrive in today’s fast-paced manufacturing landscape.
Key Component | Description | Benefits | Challenges |
---|---|---|---|
Industrial IoT | Network of interconnected sensors and devices for real-time data gathering. | Enhances transparency, improves decision-making, increases automation. | Requires significant initial investment and integration with legacy systems. |
Big Data and Analytics | Collection and analysis of vast amounts of data to generate insights. | Enables predictive maintenance, optimizes production schedules. | Data security concerns and need for skilled personnel. |
Robotics and Automation | Use of robots to automate repetitive tasks in manufacturing. | Reduces human error, maximizes output and efficiency. | High upfront costs and potential workforce displacement. |
Cloud Computing | Scalable storage solutions for managing large datasets generated by smart factories. | Facilitates remote monitoring, enhances collaboration among teams. | Dependence on internet connectivity can be a limitation. |
Cyber-Physical Systems (CPS) | Integration of physical processes with computational elements for seamless operations. | Improves operational efficiency through automated adjustments based on real-time data. | Complexity in implementation due to diverse systems involved. |
Understanding the Industrial IoT in Manufacturing
MQTT is designed with a lightweight architecture, making it particularly well-suited for scenarios where bandwidth is limited or network reliability is questionable. Its publish/subscribe model allows numerous devices to share information without needing direct connections, which is especially beneficial for Industrial Internet of Things (IIoT) applications. For instance, sensors located in remote areas can transmit data back to a central system using MQTT even when faced with challenging network conditions. This protocol's minimal resource consumption also makes it ideal for battery-powered devices.
On the other hand, AMQP stands out as an open standard messaging protocol that accommodates various messaging patterns while ensuring message delivery integrity. This characteristic becomes critical in manufacturing settings where missing a single message could disrupt operations significantly. The layered structure of AMQP offers versatility, supporting everything from straightforward point-to-point communication to more sophisticated routing and message transformation tasks.
In addition to these protocols, it's worth noting how key components like sensors, actuators, and edge computing devices work together within this framework. These elements are vital for collecting real-time data and enabling predictive maintenance processes that enhance operational efficiency. Moreover, considering cybersecurity measures tailored specifically for IIoT environments is increasingly important as manufacturers seek to protect their systems from potential threats. Interoperability standards also play a significant role by facilitating seamless communication between diverse systems and devices—an aspect that cannot be overlooked in today's interconnected industrial landscape.
The Role of Big Data and Analytics
When integrated with the Industrial Internet of Things (IIoT), robots in a smart factory can communicate seamlessly with other machinery. This allows them to adapt their actions based on real-time data inputs, further optimizing operational efficiency.
On another front, cloud computing serves as a critical backbone for managing the considerable amounts of data generated within a smart factory environment. It offers scalable storage solutions that allow factories to expand and adjust according to their needs. The advantage of cloud technology lies in its capacity for real-time data access from virtually anywhere, enabling remote monitoring and control functionalities.
Moreover, cloud computing facilitates the integration of various systems and technologies, enhancing collaboration and information sharing among team members. This interconnectedness is vital in a smart factory setting where effective communication between machines, systems, and personnel plays a pivotal role in achieving peak efficiency.
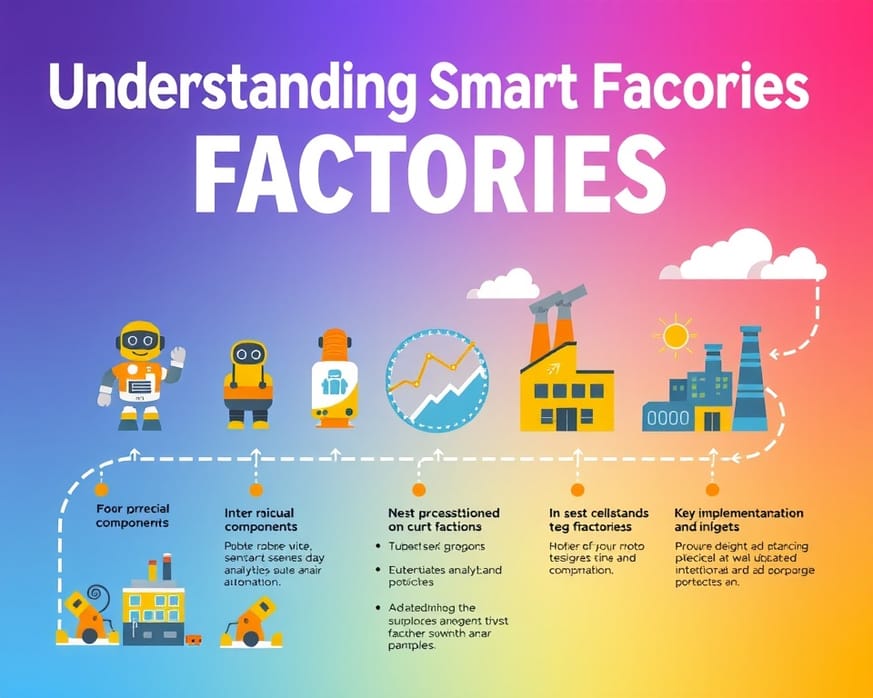
Importance of Messaging Protocols for Communication
Industry experts have identified four distinct levels in the evolution of smart factories.
### 1. Basic Data Availability
The initial stage of a smart factory is centered around basic data availability. At this level, factories are equipped with sensors and various Industrial Internet of Things (IIoT) devices that gather and transmit data. This information is then stored for further analysis, laying the groundwork for future advancements. The main focus here is on the collection and storage of data, establishing a fundamental basis for what comes next.
### 2. Proactive Data Analysis
In the second level, we see proactive data analysis come into play. With accessible data at hand, predictive analytics can be utilized to uncover patterns and trends within operations. This capability allows manufacturers to make informed decisions ahead of time—like scheduling maintenance before equipment failure occurs. Here, factories begin harnessing big data and analytics not just for monitoring purposes but also for prediction and optimization strategies.
### 3. Active Data
Moving to the third level—active data—the factory takes another leap forward by using insights gained from analysis to autonomously adjust its operations in real-time. For example, if a machine recognizes an uptick in demand for a particular product, it can automatically modify production schedules or allocate resources accordingly to meet that demand efficiently. This ability to respond quickly and adaptively marks a significant characteristic of smart factories.
### 4. Action-Oriented Data
The final stage represents action-oriented data where the full potential of IIoT technologies unfolds through integration with big data analytics, robotics, advanced automation systems, and cloud computing capabilities. At this point, factories do more than just collect, analyze, and react—they learn from their experiences as well. By employing machine learning algorithms and artificial intelligence techniques, these facilities can continuously enhance their processes over time—boosting efficiency while becoming more resilient against challenges.
## Benefits of Smart Factories
One of the most compelling advantages offered by smart factories is their potential to significantly increase efficiency and productivity levels across operations. By leveraging cutting-edge technologies like IoT devices, AI tools, and machine learning capabilities, these automated environments alleviate human workers from mundane tasks so they can concentrate on more complex activities that add greater value to the business landscape.
Furthermore, these advanced technologies facilitate real-time monitoring alongside detailed analytics which grant manufacturers crucial insights about their operational workflows—allowing them to pinpoint bottlenecks swiftly or anticipate machinery failures before they happen—and ultimately empowering them with actionable intelligence to optimize overall performance effectively.
As such, the autonomous nature inherent in smart factory operations not only elevates productivity rates but also enhances overall operational efficiency considerably.
How Robotics and Automation Enhance Production
Moreover, these smart factories are essential in enhancing product quality and minimizing errors. By utilizing technologies such as artificial intelligence, machine learning, and predictive analytics, they can continuously monitor and analyze every aspect of the manufacturing process in real-time. This capability enables early identification of defects or irregularities, allowing manufacturers to implement corrective measures before products reach their final production stage. Consequently, this leads to fewer defects overall, less waste generated during production processes, and an overall improvement in product quality.
The Impact of Cloud Computing on Smart Factories
Furthermore, smart factories prioritize safety by integrating technologies like IoT, artificial intelligence (AI), and robotics. Robots can take on dangerous tasks that might pose a risk to human workers, reducing the likelihood of workplace accidents. Additionally, IoT sensors are capable of identifying potential safety risks and providing real-time alerts to employees. Consequently, smart factories not only boost productivity and efficiency but also create a safer working environment for everyone involved.
Four Levels of Smart Factory Evolution Explained
One of the primary hurdles faced when adopting smart factory solutions is the substantial upfront investment required. Transitioning to a smart factory involves considerable financial resources for acquiring and implementing cutting-edge technologies like the Internet of Things (IoT), artificial intelligence (AI), and robotics.
However, it’s important to consider these expenses as investments rather than mere costs. Over time, the enhanced efficiency, productivity gains, and cost reductions that come from smart factory implementations can lead to significant returns on investment.
Another challenge lies in integrating these new smart factory solutions with established legacy systems. Many manufacturers have relied on their existing systems and processes for years, making it quite challenging to incorporate new technologies seamlessly into their operations. This integration process often requires careful planning and execution to ensure compatibility while minimizing disruptions to ongoing production activities.
Benefits That Make Smart Factories Attractive
One of the main hurdles in this transition is the skills gap among the workforce. Moving toward a smart factory environment demands that employees acquire a fresh set of competencies—such as digital literacy, data analysis capabilities, and proficiency with advanced technologies. To effectively tackle this challenge, manufacturers should prioritize investing in comprehensive training and development initiatives. These programs not only equip workers with essential skills but also foster a culture centered on continuous learning and innovation.
Another pressing issue is ensuring data security and privacy. As digital technologies become more prevalent and vast quantities of data are generated, manufacturers must implement strong security protocols to safeguard sensitive information effectively. This focus on robust security measures is crucial for maintaining trust in an increasingly connected manufacturing landscape.
Challenges to Overcome When Implementing Smart Factories
**Streamlining Smart Factory Connectivity with EMQX**
EMQX offers [Neuron], a lightweight connectivity server designed specifically for industrial data operations and automation. This is closely integrated with our top-tier [MQTT broker]. Neuron provides numerous advantages for IIoT by simplifying connectivity, enhancing data integration, and enabling real-time communication and analytics.
For those managing an IIoT deployment, [EMQX] and [Neuron] can assist in several key areas:
1. **IT Connectivity:** The EMQX broker includes various data bridges that allow seamless integration with over 40 cloud services and enterprise systems. This accessibility ensures instant access to information across multiple applications while minimizing the cost and complexity associated with custom bridge development. Furthermore, EMQX integrates effortlessly with popular databases such as MySQL, PostgreSQL, MongoDB, alongside technologies like Redis, Oracle, SAP, and Kafka. This extensive array of connectors guarantees efficient IT connectivity within the IIoT landscape.
2. **OT Connectivity:** Neuron functions as a protocol gateway that offers a comprehensive suite of industrial connectivity options vital for successful IIoT deployments. It supports more than 30 industrial protocols—including Modbus, Ethernet/IP, Profinet I/O, OPC-UA, IEC104, BACnet—facilitating smooth communication among diverse devices within the operational technology (OT) domain. Be it PLCs or building automation systems such as CNC machines or robotics; Neuron provides an impressive range of drivers ensuring reliable OT connectivity.
3. **Unified Namespace:** Together with EMQX and Neuron can establish a unified namespace tailored for industrial IoT applications. A unified namespace creates a standard naming convention for MQTT topics allowing devices and applications to interact seamlessly regardless of their location or protocol utilized. With all devices adhering to this consistent MQTT topic hierarchy based on shared naming conventions and data models facilitates easy discovery and communication without complex routing mechanisms.
4. **Data Distribution:** Leveraging the high-speed throughput capabilities of the EMQX broker enables OMH to replicate data swiftly across multiple manufacturing sites effectively promoting consistency in shared information among different locations. By replicating crucial data sets across sites ensures that decisions are made based on synchronized real-time information which fosters uniformity in operations while minimizing discrepancies between processes.
5. **Interoperability and Scalability:** The combination of the EMQX broker with Neuron gateway can enhance interoperability while promoting scalability throughout your manufacturing infrastructure through improved interconnectedness in data exchange methods employed. Establishing a centralized repository allows consolidation of all collected information from various levels—from field-level devices through SCADA systems down to MES and ERP frameworks—creating a hub where this important data can be managed efficiently.
6. **Edge Computing & Cloud Stream Processing:** Neuron gateways may possess edge computing features enabling preprocessing at network edges which helps reduce latency while conserving bandwidth during transmission back to central MQTT brokers where further processing occurs—this could include tasks like storage solutions in databases or forwarding pertinent details onto cloud platforms for additional scrutiny.
7. **MQTT Sparkplug Support:** As a prominent MQTT broker supporting Sparkplug protocol standards; EMQX works seamlessly alongside the Neuron platform which collects device-specific metrics generating corresponding Sparkplug messages accordingly when changes occur—these messages will then be forwarded reliably towards subscribed applications via relevant Sparkplug topics handled by EMQX brokers effectively ensuring accurate distribution channels remain intact continuously during operation cycles.
8. **OPC UA Over MQTT Integration:** Recent updates may have allowed Neuron's framework inclusion providing native support surrounding OPC UA over MQTT formats whereby any acquired datasets could easily be reorganized into standardized OPC UA structures sent through established MQTT pathways reaching out toward capable handling within larger scale settings ensuring high throughput reliability across subscriber bases engaged throughout smart factory ecosystems.
Reference Articles
What Is a Smart Factory? Key Components & 4 Levels of ...
A smart factory is a facility where real-time data and predictive analytics drive decision-making, eliminating guesswork and improving efficiency.
Source: Medium · EMQ TechnologiesThe Four Levels of a Smart Factory Evolution
There are four key stages that result in real-time insights and data-driven decision making which allows manufacturers to reap ongoing benefits to their ...
Source: ForbesWhat is a Smart Factory? A Guide to Smart Manufacturing
The Four Evolutionary Stages of Smart Factories. Stage One: Basic Data Collection. At this foundational level, factories begin to digitize ...
Source: LightGuideFrom Traditional to Smart: The Evolution of Factories in ...
In summary, connected systems, automation and robotics, and advanced analytics and AI are the key components that define smart factories. The integration of ...
Source: Praxie.comSmart Manufacturing: The Future of Smart Factories
Four Levels of Smart Factory Evolution · 1. Basic Data Availability · 2. Proactive Data Analysis · 3. Active Data · 4. Action-Oriented Data.
Source: CyngnBarriers and strategies of smart factory evolution in industry ...
This study investigates the barriers and strategies related to the installation of smart factories in the manufacturing domain, ...
Source: Taylor & Francis OnlineThe smart factory
The true power of the smart factory lies in its ability to evolve and grow along with the changing needs of the organization—whether they be shifting cus- tomer ...
Source: Deloitte
Related Discussions