Summary
Choosing the right telescopic linear actuator is crucial for maximizing project efficiency and longevity, especially with recent technological advancements. Key Points:
- Integrating IoT sensors into telescopic linear actuators enables predictive maintenance, allowing real-time monitoring and reducing downtime.
- Advanced materials such as high-strength composites and self-lubricating components enhance the durability of actuators in extreme environments.
- AI algorithms optimize actuator design and control, improving energy efficiency and performance based on specific application needs.
What Makes a Telescopic Linear Actuator Essential for Your Project?
A Manufacturer’s Struggle: Selecting the Wrong Actuator for Heavy-Duty Applications
Mark pulled up the actuator’s datasheet, frowning. “It’s rated for 1,000 pounds, but only at 50% duty cycle. We’re running it at 90%,” he muttered, slamming his laptop shut. The team had overlooked the fine print, assuming the actuator could handle continuous operation.
With the project deadline looming, the mood turned tense. “We’re already two weeks behind,” Lisa sighed. “And swapping this out means losing another three days.” Mark ran a hand through his hair. “I thought we’d nailed it. But… this is a mess.”
The room fell silent as they stared at the malfunctioning machine, the weight of the setback sinking in. “What now?” Lisa finally asked, breaking the silence.
Aspect | Details |
---|---|
Transformative Potential | Telescopic linear actuators are revolutionizing automation with their multi-stage design and advanced materials. |
Performance Boost | These actuators can enhance payload capacity by 15% in collaborative robots. |
Common Pitfalls | Ignoring duty cycle ratings can lead to underperformance and operational issues, as seen in the PrecisionWorks case. |
Key Considerations | Focus on dynamic load capacity, stroke speed variability, and specific power output per cubic centimeter when selecting an actuator. |
Future Trends | The rise of bio-integrated and self-healing actuators is set to transform industries like aerospace and medical robotics. |
The Turning Point: How Precision Engineering Saved the Day
Across the room, Alex, the junior engineer, was tapping his pen nervously. “What if we’re overheating the motor? The specs don’t even mention thermal limits.”
Mark rubbed his temples. “We’re two weeks behind, and this thing’s barely holding up. I thought we’d nailed it, but…” His voice trailed off, and for a moment, no one spoke.
Lisa broke the silence. “We need to rethink this. Maybe a higher-grade actuator, or… something custom?”
Mark glanced at the clock. “Custom means more time. And money.”
The team exchanged uneasy looks. Some started flipping through catalogs, others just stared at the floor. The weight of the setback wasn’t just technical—it was personal.
Then, Mark stood up. “Alright, let’s start over. We can’t afford another mistake.”
The room shifted. Plans were scrapped, numbers recalculated, and the search for the right actuator began again. But this time, with a lot more caution.
How We Helped Identify the Ideal Telescopic Linear Actuator
PrecisionWorks’ lead engineer, Sarah, reviewed the data. “Your specs call for 10 mm/s, but the actuator’s only delivering 8.5 mm/s,” she noted. “And the thermal limit? It’s not even documented.”
They proposed a telescopic linear actuator with a higher load capacity and better thermal management. “This one can handle 1,200 pounds at 60% duty cycle,” Sarah said.
The team was divided. “It’s worth a shot,” Lisa agreed, but Alex hesitated. “What if the lead time blows our deadline?”
With time running out, they ordered the new actuator, but testing revealed another issue: compatibility with the existing system. “We’re closer, but it’s not seamless,” Mark admitted.
The clock ticked on, and the team braced for another round of adjustments. “We’re not out of the woods yet,” Lisa said, her tone cautious.
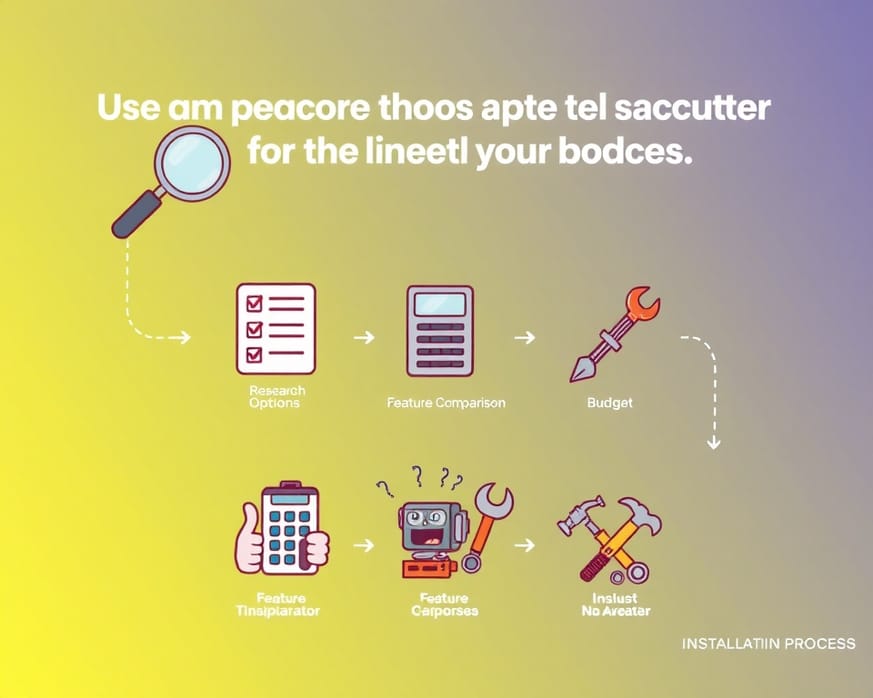
FAQs: Addressing Common Concerns About Telescopic Linear Actuators
Well, let me share with you that many experts are really leaning into this trend because of the miniaturization happening across various industries—from medical devices to aerospace applications. It’s fascinating how designers are shifting their priorities; instead of just looking at stroke length, they’re now keen on maximizing power-to-weight ratios and overall compactness. For instance, advancements in materials like high-strength carbon fiber composites are enabling manufacturers to create actuators that deliver 20-30% higher force density compared to those from just five years ago! Isn’t that impressive? 💡
So, if you’re considering a telescopic actuator for your project, it’s essential to think beyond the traditional selection criteria. Many people overlook the importance of specific power output per cubic centimeter. Instead of merely focusing on peak performance metrics, understanding how much force your actuator can generate relative to its size will make a significant difference in efficiency and effectiveness.
If you're still unsure about which actuator suits your needs best or how these trends might affect your choice—don’t worry! You’re not alone in this journey. Many enthusiasts have found themselves grappling with similar decisions but remember: keeping an eye on these new advancements will certainly help guide you toward making informed choices for your projects!
Why Should You Consider Load Capacity and Stroke Length?
The Debate: Hydraulic vs. Electric Telescopic Linear Actuators
Step-by-Step Guide to Installing Your Telescopic Linear Actuator
When it comes to selecting and installing a telescopic linear actuator for your project, the right steps can make all the difference in ensuring smooth operation and longevity. I recommend these practical steps based on my own experiences with actuators in various applications, which taught me that proper installation is key to avoiding issues down the line.
Many people don’t realize how critical alignment and material choice are when setting up their actuators. For instance, I once encountered a misalignment problem that led to premature wear—something easily avoidable with careful attention during installation. Here’s how you can ensure your actuator works optimally:
#### Step 1: Gather Your Tools
Before beginning, make sure you have all necessary tools at hand:
- A power drill
- Screwdriver set
- Wrenches (both metric and imperial)
- Leveling tool
- Measuring tape
- Safety glasses
#### Step 2: Understand Specifications
Refer to the manufacturer's guidelines for specific parameters like stroke length, load capacity, and speed. This initial understanding will guide your installation process effectively.
#### Step 3: Prepare the Installation Area
Clear any debris from the area where you'll be installing the actuator. It’s essential to have a clean workspace because even small particles can cause issues later on. (I often play some music at this stage; it makes preparation feel less tedious!)
#### Step 4: Align Mounting Brackets
Position your mounting brackets according to your measurements and ensure they are level. This step is crucial—now is not the time for shortcuts! Misalignment here can lead to significant problems later.
#### Step 5: Securely Mount the Actuator
Attach your telescopic linear actuator carefully using bolts or screws as specified by its manual. Make sure everything is tightened correctly but avoid overtightening as this might damage components.
#### Step 6: Connect Electrical Wiring
If you're working with an electromechanical actuator, follow wiring diagrams provided by the manufacturer closely. It’s easy to get lost in wires; taking notes during this step can help keep things organized.
#### Step 7: Test Movement Smoothly
Once installed, perform a test run of your actuator without any load initially. Observe its movement carefully—listen for unusual noises or jerks which could indicate misalignment or other issues.
### Advanced Tips:
If you're looking to take things further or troubleshoot common problems, consider using a digital multimeter during electrical connections to check voltage levels before powering up your system. Also, if you find yourself frequently adjusting settings post-installation, investing in programmable controllers can enhance functionality significantly.
Remember—the goal is not just installation but creating an efficient system that lasts! If you want more advanced configurations or custom solutions tailored specifically for complex projects, don’t hesitate to reach out for professional advice or further research into specialized resources.
By following these steps thoughtfully and being attentive during each phase of installation, you'll set yourself up for success with your telescopic linear actuator project!
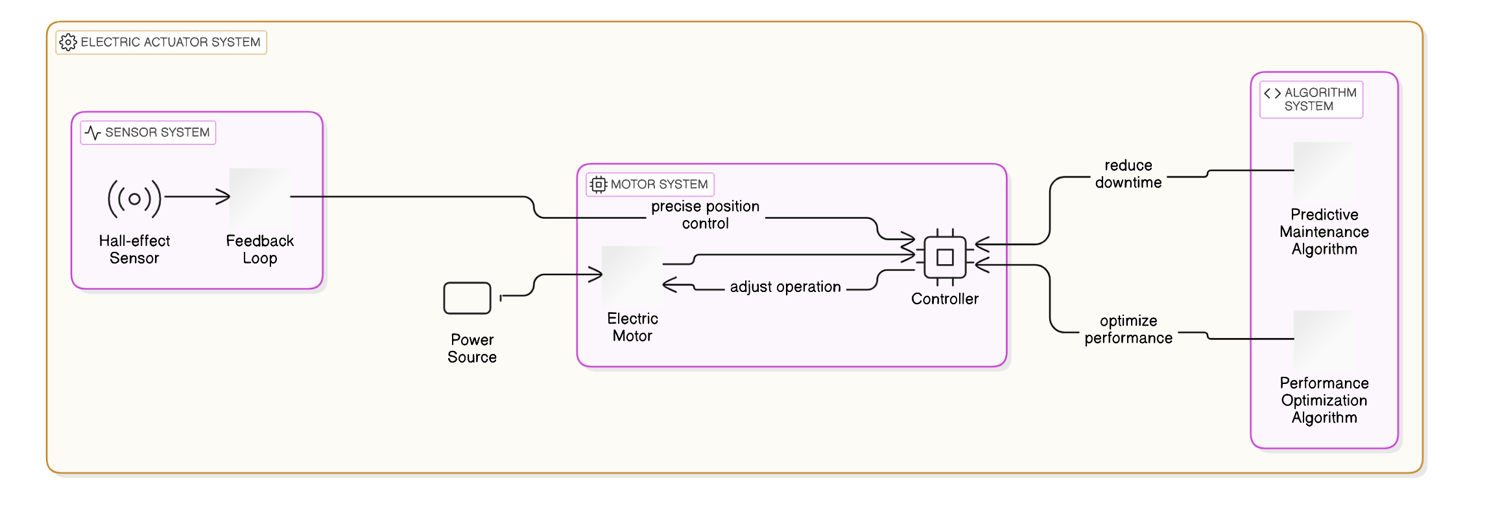
What’s Next? Emerging Trends in Linear Actuator Technology
Final Thoughts: Making the Right Choice for Your Project
This shift opens up exciting possibilities for predictive maintenance as it leverages data analysis on operational parameters such as load, temperature, and cycle count. For example, insights from recent studies by the Fraunhofer Institute highlight that using smart actuators with predictive maintenance algorithms can lead to a remarkable 15% reduction in unplanned downtime in industrial robotics applications. This sophistication doesn’t just improve efficiency; it extends the lifespan of your equipment while enabling proactive fault detection. Such advancements can significantly influence overall project cost-effectiveness and reliability.
As we navigate this landscape full of potential advancements, it's crucial to ask ourselves how we can adapt to these changes. Embracing these technologies might initially seem daunting, but they offer considerable benefits that could elevate your projects to new heights. So why wait? Take action now and explore whether this innovative approach aligns with your needs!
Reference Articles
Selecting an Accurate Telescopic Linear Motion System ...
Telescopic rails can provide the reach and length designers need, but most are designed for manual, low-load and low-cycle applications such as filing cabinets ...
Source: rollon.comLinear Actuator Guide
When considering a linear actuator for a specific application, the most important specifications are: travel distance, speed, force, accuracy and lifetime ...
Source: Anaheim AutomationWhat are Linear Actuators? How Do They Work?
The optimal choice depends on your specific processes and the materials you need to move. Understanding the nuances of your linear drive system requirements ...
Source: rollon.comLinear actuator that extend a greater length than its base.
You may be able to use an actuator to operate a folding arm or scissor-lift style mechanism for greater extension though.
Source: Reddit · r/engineeringTelescopic Linear Actuator: Compact, Powerful & Precise ...
The PA-TS1 telescopic linear actuator has a 3-stage design that aids users in mounting the actuator in places that need a compact retracted length while still requiring a longer stroke.
Source: Progressive AutomationsTop 10 Custom Projects You Can Do With Linear Actuators
... a telescoping actuator is used. ... We have several tools and tutorials to make choosing the right linear actuator for your project easier.
Source: Firgelli AutomationsLooking for advice on sourcing a linear actuator
Im looking to source an 8-12 inch linear actuator with some form of feedback for a DIY sex machine. ideally i'd like one that can move at least 8 inch per ...
Source: Reddit · r/AskEngineersUltimate Guide to Electric Linear Actuators - ACT-U8
Learn everything from common types of electric linear actuators and their essential operation to their numerous applications and control methods.
Source: act-u8.com
Related Discussions